Emma was able to come up with a new design for the bracelet, deciding to make it into a cuff and have all of the pieces put together and printed all at once instead of in pieces. Keegan was able to help with making the design come to life using NX in the ME building. The bracelet is still printing and will be ready in 5.5 hours as of now.
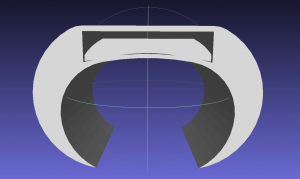
We also decided to add a circular part to the top of the bracelet that can hopefully be pushed down onto the button for the 3 seconds.
Once it finishes printing, the next steps are to evaluate how well the tech will fit inside of the new design and go from there. Hopefully we won’t have to print another one but if we do, we would have to have it done by Thursday night.
This week Keegan kept working on the Simblee application for Sirena. Coming down on our last week we’ve decided to go to our fall back plan for the app. Right now the idea is to create a dummy app that will look like a functioning app and an alert will pop up when the button on the bracelet is held saying that you have sent a text notification, but with limited time and coding knowledge the app will not actually send an email or text, it will just look like it did. I hope to get that functionality put in to action by Tuesday or Wednesday of this week and can take one last crack at trying to send an email for some proof of concept.
Emma was also able to get the poster ready…all we need is images of the final bracelet which we don’t have just yet. 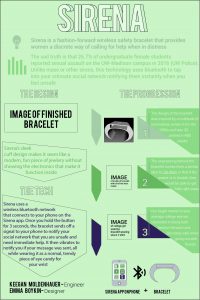